Evolution of Electric Screw Press
Author: Zhengzhou Haloong Machinery Manufacturing Co., Ltd. Time: 2017-05-18 11:40
Screw press is one of the oldest forming equipment, has a very long history of development. A long time ago, there was a wooden screw press in Europe to suppress grape juice and olive oil. 15th century German Johann Gensleisch made a spiral press on a wooden screw press, which can be said to be the ancestors of screw press and other mechanical presses. In the European language, the press and the printing of the two words have the same root. At the beginning of the 16th century, the Italians used metal presses to suppress metal works of art and coins. Figure 1 for the 18th century by the man-driven screw press. Until the mid-19th century there was a steam-driven mechanical press.
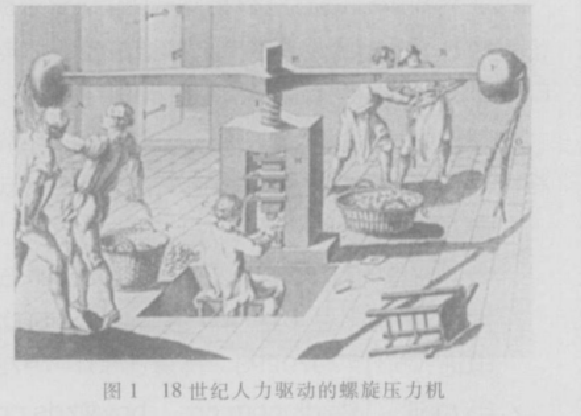
The first screwdriver is driven by friction plate transmission power in modern industrial production, referred to as friction press, which began in the early 19th century, because the structure is simple, reliable, friction press is still in use. The biggest drawback is the low efficiency of friction transmission, about 50% to 55%, the total efficiency of about 20% to 25%. In the past century, people have been looking for improved methods, the main objectives are: 1. To improve transmission efficiency, reduce energy consumption; 2. Increase equipment tonnage, improve work ability; 3. Improve the combat energy control accuracy and operation of the degree of automation
The twentieth century is the period of rapid development of screw press. In the 1920s, people began to develop hydraulic screw press, and were put into industrial applications in the late 1940s. In 1930s, the former Soviet Union began the development of electric screw press, the late 50s began to product product in Germany, to the late 70s, Germany Simpei company developed a successful clutch screw press. At the end of the 20th century, Japan Enomoto company developed a servo drive motor screw press.
Into the 21st century, the spiral press this old forming equipment is still booming, has formed a variety, complete specifications, the degree of automation is gradually high and continues to contribute for the development of human civilization.
Several typical screw press:
Friction presses:
Friction press is the earliest emergence of modern industrial screw press, it has a simple structure, the advantages of low prices, so far nearly 200 years of history and still in use, in addition to forging industry, but also used in the building materials industry.
The main problem with the friction press is that the motor needs to drive the friction plate to always rotate at high speed, and the flywheel needs to change the direction of rotation in one cycle, and the flywheel and the friction plate in the commutation cause serious slip. This not only reduces the transmission efficiency, but also exacerbates the friction belt wear, thereby increasing the manufacturing and maintenance costs, can not be widely used. Friction presses are inefficient and the impact control is inaccurate and is not suitable for large tonnage.
Clutch type screw press:
The frequent reversing of a large inertia flywheel is the main reason for the inefficientness of the screw press, since a large amount of energy is consumed during the acceleration deceleration and braking process. In 1979, a clutch was connected between the flywheel and the screw, which is similar with Crank-type presses, there has been a clutch-type screw press. The flywheel in the course of work has always been rotated in one direction, without stopping and reverse, size and moment of inertia can be much larger than ordinary friction press. When the need to strike, the clutch is combined, because the clutch by the screw side of the part of the inertia of inertia is specially short , in a very short period of time to reach the rated speed. During the forming process, the flywheel decelerates the release of energy until the clutch slips, and then the clutch is quickly disengaged, the cylinder pushes the slider, the screw rises rapidly and returns to its original position, and the impact force and energy are controlled by the clutch. Generally when the flywheel deceleration to reach 12.5% to achieve the maximum impact force.
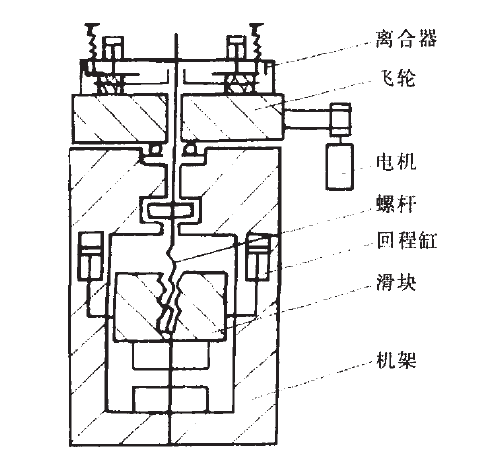
Clutch-type screwpress is a very successful improvement to the friction press, the main advantages are: 1. High efficiency, more than 60% to 40% of the friction pressure function; 2. Strike energy, is the friction press 3 times, so also known as high-energy friction press; 3 can be in the large stroke range to obtain the maximum impact force and the maximum forming speed. At present, the domestic clutch design tonnage has reached 6300KN.
Electric screw press:
Using a motor rotor instead of a flywheel, or by a gear or belt to drive the flywheel to rotate, the inefficient friction drive is removed, with the shortest drive chain and higher efficiency. The former Soviet scholar based on these ideas, in 1933 developed a direct drive motor 2000KN screw press testing machine. But because the motor is in the positive - reverse and start - stop working state, fever is very serious, the temperature rose to 120 degrees Celsius, in view of the current level of motor and control technology, this problem can not be solved, the development work had failed.
The initial electric screw press machine did not get the expected effect, there are two reasons: 1. Motor frequent start and stop, power loss more than 50%, the motor fever is serious; 2. Start current is too large (is 3 ~ 5 times of stable load), a huge impact on the power grid, although the single motor drive into more than one motor drive, made the situation can improved, but still can not fundamentally solve the problem.
Since the end of the 20th century, due to power electronics technology, motor technology, computer control technology has got rapid development, which has brought an opportunity for solving the problem of electric screw press. After a long period of development and development, Zhengzhou Hualong Machinery Manufacturing Co., Ltd. in the early 21st century produced by the electric screw presses using frequency conversion technology, successfully produced in line with the efficient production of electric screw press, the main advantages are: 1 . The use of frequency conversion technology to make the motor always in the best condition work, not only the current was greatly reduced, and the heat was greatly reduced; 2. Filter to start the current impact on the power grid to further reduce; 3. Reduce the current loss. Electric screw press not only greatly improve the control of the entire equipment level and combat energy, other parameters can also be more precisely controlled. This is the spiral press to the more large-scale, energy-saving out of the road.
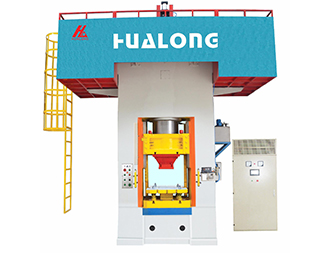
Electric screw press is a very suitable process forging equipment. Spiral presses are omnipotent, simple structure, easy adjustment and maintenance, slider without bottom dead center, easy to design molding, high precision forgings. Applicable to all kinds of precision forging, finishing, fine pressure, embossing, calibration, school leveling and other processes, is a landmark product in the field of spiral press.
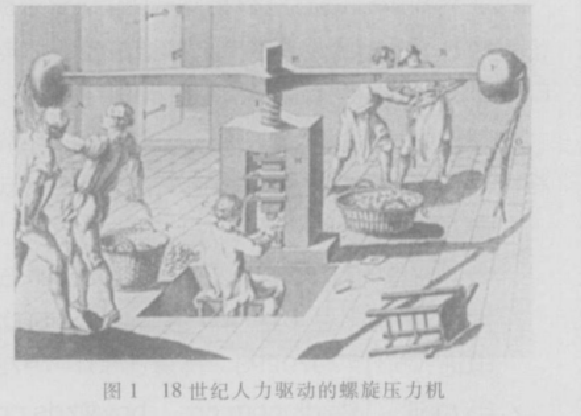
The first screwdriver is driven by friction plate transmission power in modern industrial production, referred to as friction press, which began in the early 19th century, because the structure is simple, reliable, friction press is still in use. The biggest drawback is the low efficiency of friction transmission, about 50% to 55%, the total efficiency of about 20% to 25%. In the past century, people have been looking for improved methods, the main objectives are: 1. To improve transmission efficiency, reduce energy consumption; 2. Increase equipment tonnage, improve work ability; 3. Improve the combat energy control accuracy and operation of the degree of automation
The twentieth century is the period of rapid development of screw press. In the 1920s, people began to develop hydraulic screw press, and were put into industrial applications in the late 1940s. In 1930s, the former Soviet Union began the development of electric screw press, the late 50s began to product product in Germany, to the late 70s, Germany Simpei company developed a successful clutch screw press. At the end of the 20th century, Japan Enomoto company developed a servo drive motor screw press.
Into the 21st century, the spiral press this old forming equipment is still booming, has formed a variety, complete specifications, the degree of automation is gradually high and continues to contribute for the development of human civilization.
Several typical screw press:
Friction presses:
Friction press is the earliest emergence of modern industrial screw press, it has a simple structure, the advantages of low prices, so far nearly 200 years of history and still in use, in addition to forging industry, but also used in the building materials industry.
The main problem with the friction press is that the motor needs to drive the friction plate to always rotate at high speed, and the flywheel needs to change the direction of rotation in one cycle, and the flywheel and the friction plate in the commutation cause serious slip. This not only reduces the transmission efficiency, but also exacerbates the friction belt wear, thereby increasing the manufacturing and maintenance costs, can not be widely used. Friction presses are inefficient and the impact control is inaccurate and is not suitable for large tonnage.
Clutch type screw press:
The frequent reversing of a large inertia flywheel is the main reason for the inefficientness of the screw press, since a large amount of energy is consumed during the acceleration deceleration and braking process. In 1979, a clutch was connected between the flywheel and the screw, which is similar with Crank-type presses, there has been a clutch-type screw press. The flywheel in the course of work has always been rotated in one direction, without stopping and reverse, size and moment of inertia can be much larger than ordinary friction press. When the need to strike, the clutch is combined, because the clutch by the screw side of the part of the inertia of inertia is specially short , in a very short period of time to reach the rated speed. During the forming process, the flywheel decelerates the release of energy until the clutch slips, and then the clutch is quickly disengaged, the cylinder pushes the slider, the screw rises rapidly and returns to its original position, and the impact force and energy are controlled by the clutch. Generally when the flywheel deceleration to reach 12.5% to achieve the maximum impact force.
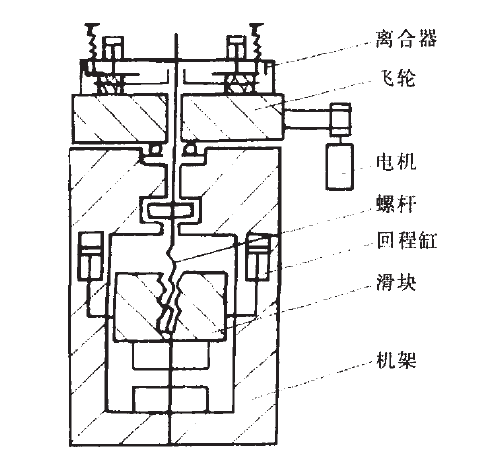
Clutch-type screwpress is a very successful improvement to the friction press, the main advantages are: 1. High efficiency, more than 60% to 40% of the friction pressure function; 2. Strike energy, is the friction press 3 times, so also known as high-energy friction press; 3 can be in the large stroke range to obtain the maximum impact force and the maximum forming speed. At present, the domestic clutch design tonnage has reached 6300KN.
Electric screw press:
Using a motor rotor instead of a flywheel, or by a gear or belt to drive the flywheel to rotate, the inefficient friction drive is removed, with the shortest drive chain and higher efficiency. The former Soviet scholar based on these ideas, in 1933 developed a direct drive motor 2000KN screw press testing machine. But because the motor is in the positive - reverse and start - stop working state, fever is very serious, the temperature rose to 120 degrees Celsius, in view of the current level of motor and control technology, this problem can not be solved, the development work had failed.
The initial electric screw press machine did not get the expected effect, there are two reasons: 1. Motor frequent start and stop, power loss more than 50%, the motor fever is serious; 2. Start current is too large (is 3 ~ 5 times of stable load), a huge impact on the power grid, although the single motor drive into more than one motor drive, made the situation can improved, but still can not fundamentally solve the problem.
Since the end of the 20th century, due to power electronics technology, motor technology, computer control technology has got rapid development, which has brought an opportunity for solving the problem of electric screw press. After a long period of development and development, Zhengzhou Hualong Machinery Manufacturing Co., Ltd. in the early 21st century produced by the electric screw presses using frequency conversion technology, successfully produced in line with the efficient production of electric screw press, the main advantages are: 1 . The use of frequency conversion technology to make the motor always in the best condition work, not only the current was greatly reduced, and the heat was greatly reduced; 2. Filter to start the current impact on the power grid to further reduce; 3. Reduce the current loss. Electric screw press not only greatly improve the control of the entire equipment level and combat energy, other parameters can also be more precisely controlled. This is the spiral press to the more large-scale, energy-saving out of the road.
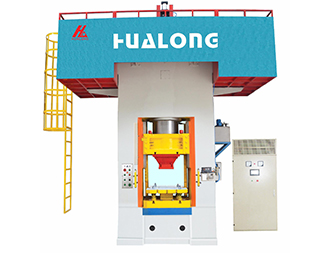
Electric screw press is a very suitable process forging equipment. Spiral presses are omnipotent, simple structure, easy adjustment and maintenance, slider without bottom dead center, easy to design molding, high precision forgings. Applicable to all kinds of precision forging, finishing, fine pressure, embossing, calibration, school leveling and other processes, is a landmark product in the field of spiral press.